Stainless steel: The role of nickel
Release date: 2021-1-6 9:24:24 Visits: 959
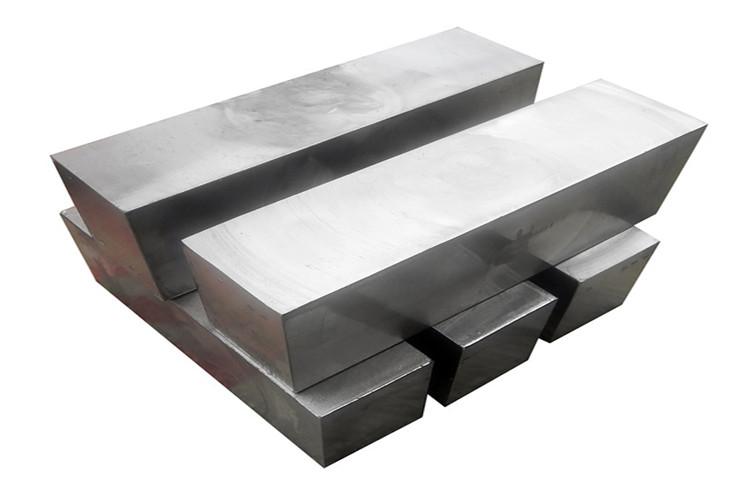
Formability
The austenitic structure provides stainless steels with good ductility and formability. The common 18% chromium/ 8% nickel Type 304 in particular shows good stretch-forming characteristics. A slightly higher nickel content further increases the stability of the austenite and reduces the work-hardening tendency, increasing suitability for deep drawing. Unlike low-nickel, high-manganese alloys, these alloys are not prone to delayed cold cracking. Their excellent formability has led to 300-series austenitic alloys being widely used for items such as kitchen sinks and cooking pots.
Weldability
Many pieces of stainless steel equipment are fabricated by welding. In general, nickel austenitic alloys are better for welding than other alloys, with Types 304 and 316 being the most widely-fabricated stainless steels in the world. Unlike ferritic alloys, they are not prone to brittleness as a result of high-temperature grain growth and the welds have excellent bend and impact properties. They are readily weldable in both thick and thin sections.
Toughness
Toughness - the ability of a material to absorb energy without breaking - is essential in many engineering applications. Most stainless steels have good toughness at room temperature, however, as temperature decreases the ferritic structure becomes progressively more brittle, making ferritic stainless steels unsuitable for use at cryogenic temperatures. In contrast, the common austenitic stainless steels retain good toughness even at liquid helium temperatures (-270oC), which is why grades such as Type 304 are widely used for cryogenic applications.
High-temperature properties
Adding nickel gives the austenitic alloys of stainless steel significantly greater high-temperature strength than other alloys, particularly the ability to resist the tendency to move slowly or deform permanently under mechanical stresses, known as creep. These alloys are also much less prone to forming damaging brittle phases when exposed to temperatures in excess of 300oC. Nickel also stabilises the protective oxide film and reduces spalling during thermal cycling. This is why austenitic alloys are preferred for high-temperature applications and where fire resistance is needed.
Sustainability
Most nickel-containing materials are fully recyclable at the end of the product’s useful life; indeed their high value encourages recycling. This, in turn, lessens the environmental impact of nickel-containing stainless steels by reducing both the need for virgin materials and the energy that their production uses. For example, the amount of stainless steel scrap currently being used reduces the energy required for stainless steel manufacture by around one-third over using 100% virgin materials.
The durability of stainless steels can be seen in buildings. The restorations of St Paul’s Cathedral and the Savoy Hotel canopy in London, U.K. (1925 and 1929 respectively), the Chrysler Building in New York City and the Gateway Arch in St Louis in the U.S.A (1930 and 1965), the Progreso Pier in Mexico’s Yucatan state (c. 1940) and the Thyssen Building in Düsseldorf, Germany (1960) all testify to the longevity that can be expected from nickel-containing stainless steel.
Ease of production
Ease of production is not something that is immediately apparent to the end user. However, long experience of manufacturing the common austenitic alloys, their widespread use, their versatility and the scale of their production have allowed them to become widely and economically available in all shapes and quantities and in all parts of the world.